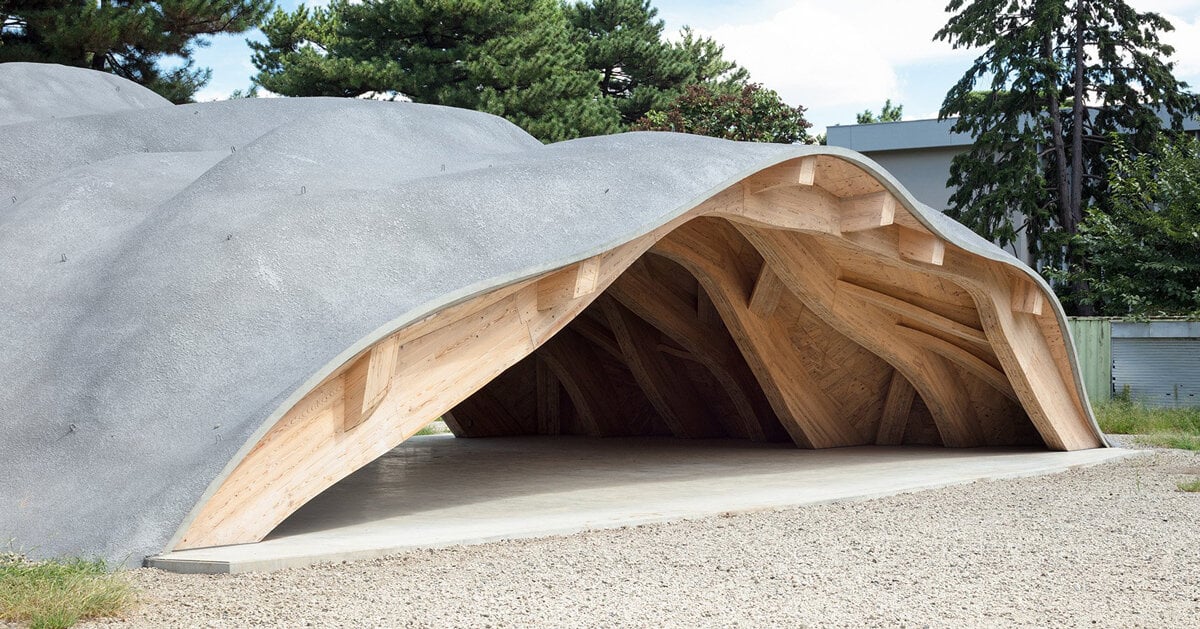
VUILD has crafted a parametric space named The Learning Architecture for Learners, designed as an open laboratory where anyone can experience advanced manufacturing technology. Initiated by the Educational Incubation Center Explayground at Tokyo Gakugei University, Japan, the structure takes shape as an organic roof, utilizing reinforced concrete and cross-laminated timber (CLT) as formwork. It incorporates CNC-machined wood beams and panels to create a distinctive finished surface referred to as ‘residual formwork.’ VUILD’s parametric team employs a geometric algorithm to generate a CAD model, facilitating the creation of a CAM path for 5-axis CNC machining. Pre-cut components are manufactured in VUILD’s factory using a 5-axis CNC machine and later installed in the completed building. The building aims to function as an open facility, providing individuals with the opportunity to engage with advanced manufacturing technology and actively participate in creating their own spaces.
roof shape that mimics the veins of leaves found in nature, all images by Takumi Ota
Formulating Innovative Learning Spaces
The design challenge was to create an open, adaptable space for new public education, serving as both a learning environment and an expandable, formless area. VUILD (see more here) opted for a large-span versatile space using a 5-axis CNC milling machine. The constraint was cutting CLT panels up to 240 mm thick, requiring repeated simulations to optimize overall shape and cut-out convenience, considering construction logistics. CLT beams were designed with a sine curve in the longitudinal section, creating a strong shell with a roof shape mimicking leaf veins. The shell’s depth was achieved with a zigzag pattern in the cross-section, and strength was added by shifting phases in three layers. The 3D CLT panels were cut in VUILD’s factory, joined on-site to the beams, and connected with metal fittings.
Concrete was poured into the beams, forming beams on the veins and an 8 cm thick slab covering the spaces. This innovative construction method has been patented as JP 2021-042568, reducing costs to 60% of the normal shell construction method. Streamlined digital fabrication with 5-axis machining features required optimization, with paths created specifically for 5-axis cutting. A parametric team developed a geometric algorithm for free-form surfaces, enabling automatic generation of CAD documents. Path creation flow was designed to minimize manual machining. An algorithm for automatic panel placement and shape generation efficiently placed parts in different thicknesses of CLT panels, facilitating optimization for both structure and construction convenience.
large openings allow for indoor/outdoor connections. The site surrounding the building has plenty of room for future expansion
the building will be used as an open laboratory where anyone can experience advanced manufacturing technology