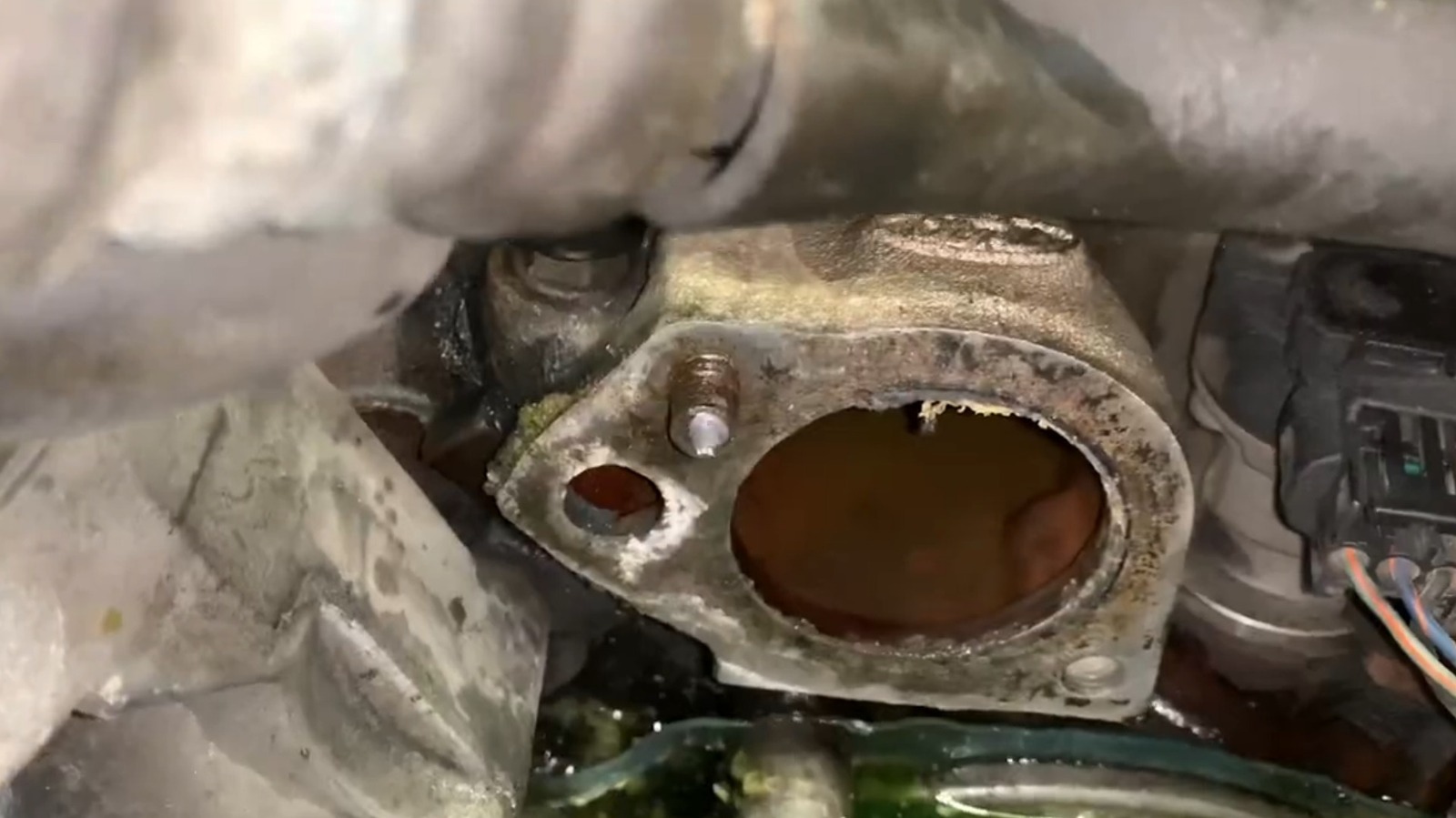
If you’ve ever dabbled in auto repair or engine tinkering, you may understand just how frustrating a broken bolt can be. It’s already difficult to remove old bolts from an engine, thanks to things like rust, corrosion, and defects caused by extreme heat. However, removing a broken bolt is a different beast entirely. That’s because broken bolts are usually missing their hex heads, meaning there’s nothing for you to grab onto with your ratchet or wrench. It’s extremely difficult to remove bolts that have broken this way, and if it happens to you while performing maintenance or repairs, you may end up stuck for days until you can remove the broken fastener.
That said, it is possible to remove a broken bolt from an engine. You may need access to some specialty mechanic’s tools, though, like a tap and die set or some extractors. Fortunately, we here at SlashGear can help break it down for you. As a former professional auto mechanic who has broken his fair share of bolts, I’ll explain the most common and effective ways to remove busted fasteners from an engine or any other component. We’ll cover various methods you can try, how to perform the steps, as well as the tools you’ll need for each. So, from using an acetylene torch and vice grips to drilling out the old part, here are five ways to remove a broken bolt from an engine.
Try applying some heat, and then use a set of vice grips
If you have a broken bolt — or even just a seized one — one of the first and simplest methods you should try to break it free involves using heat and some vice grips. The most popular heat source used for this method is an oxy-acetylene torch, but you can try various other tools, like a propane torch or even a butane torch lighter in a pinch. The idea is to make the metal extremely hot, which causes it to expand and can help break the bolt free from rust and corrosion.
To try this method, you’ll need a tool to heat the bolt. As mentioned, an oxy-acetylene torch is the most common way to perform this procedure, but you can try various other devices — just be sure to protect any surrounding components that you don’t want to heat, like rubber hoses or belts. You’ll also need something to grab the broken bolt once it’s hot. Vice grips are one of the best options, as they allow you to lock onto the bolt with extreme force. However, you can also try normal pliers or a specialized set of screw extraction pliers. Once you have your tools, it’s as simple as heating the bolt until it’s red-hot. Then, simply lock onto the broken shaft with your vice grips or pliers and try to twist it out like normal.
Note that this method will not work if the bolt breaks off flush with the hole. A small amount of the bolt must be exposed. Otherwise, you won’t be able to grab onto it with pliers or vice grips once it’s hot.
Use a hammer and chisel
If a larger bolt breaks off with a decent portion of the shaft exposed, you can try to remove it with a hammer and chisel. This is a quick and easy method you can try before moving on to more advanced and technical tactics. To give it a try, all you’ll need is a hammer — preferably a small sledge, but a standard framing or claw hammer may also work — a chisel or pry bar with a striking surface, and some penetrating oil.
Once you’ve got your tools, spray a bit of oil onto the shaft and place the sharp end of your chisel on the top side of your broken bolt. Angle your chisel so that striking it will, in theory, cause the broken bolt to twist in its loosening direction (for most standard bolts, this is left). After lining up your chisel, tap it with your hammer lightly a few times to notch the broken bolt — this will help prevent the chisel from slipping off and hitting another component. Then, give the chisel a few hard hits with your hammer. While doing so, try to avoid swinging the hammer wildly. Make controlled, steady movements, and try to direct all of the force into the chisel, in the proper direction.
After you hit the chisel a few times, try removing the bolt with a pair of pliers or vice grips. The hammer and chisel part is to break the bolt free from any corrosion or rust, but you’ll still need something else to remove the broken shaft.
Try welding a nut onto the exposed shaft
Our next method is a bit more complicated and requires access to a welding machine. Most people choose to use a wire-fed, MIG welder, but you can use a stick or arc welder, too. Besides a welding machine, you’ll also need something like a wire brush or some type of power grinder to clean the broken bolt and nut before welding them together, as well as the wire or electrodes to use with the machine.
As far as the nut goes, it can really be any nut that fits onto the broken shaft. The threads do not have to match the broken bolt, but it will help if they do. That said, if the nut is significantly larger than the broken shaft, you’ll probably be better off looking for a smaller part, as it will be challenging to weld a large nut onto a thin shaft.
Once you’ve gathered your tools and parts, clean the broken bolt and nut of any grime, grease, or corrosion. Then, either thread the nut onto the broken shaft or place it on top of the broken part. With the nut securely in place, tack weld it onto the broken bolt in at least two places. After the nut is securely attached to the broken bolt, grab your ratchet or wrench and try to remove the bolt using the nut you welded onto it.
Drill it out with a left-hand drill bit
If you’ve exhausted all of your other options, there are a couple of final methods you can try to remove a broken bolt from an engine or any other component. The next tactic we’re going to discuss involves using a punch tool, a hammer, a drill, and a left-hand or reverse-thread drill bit.
To begin, place your punch tool as close to dead center on the broken bolt shaft as possible. Then, carefully strike the punch with your hammer so that it leaves an indentation in the shaft. The indentation is to help you get the drill bit started, and it’s vital that you place it as close to perfectly centered as possible. Once you’re confident about your indentation placement, it’s time to start drilling. Line your left-hand drill bit up with the indentation you created and start boring a hole carefully — note that if your left-hand bit is very large, you may need to drill a smaller pilot hole first.
If you’re using a reverse-thread bit and the fastener has standard right-hand threads, the bit may be able to bite into the broken bolt and start twisting it out. If this tactic doesn’t work, keep drilling anyway, because you can use the hole you drill for our next and final method — just be sure to make the hole as straight and centered as possible.
Try an extractor tool
When all else has failed, you can try one final method to remove a broken bolt from your engine. Note that this tactic is pretty advanced and may not be ideal for car novices and inexperienced DIYers. That said, it is possible for anyone to perform this procedure, as long as they follow the right guidance. As with the previous method, you’ll need a punch tool, some high-quality, extra-hard drill bits if you haven’t already bored a hole with a left-hand bit, and an extractor set. You’ll also want some basic hand tools, like a hammer and a ratchet or wrench.
When you have your tools, the first step is to create an indentation as close to the center of the broken bolt shaft as possible. To do this, use your punch and a hammer. Carefully line up the punch before striking it, as you want the indentation to be as close to perfectly centered as possible. Then, grab one of your smallest drill bits and start boring a pilot hole into the broken shaft. While doing this, be extremely careful to drill as straight as possible.
After drilling the pilot hole, continue enlarging it with bigger and bigger drill bits until the hole is just slightly smaller than the extraction tool you plan to use. Next, grab your extraction tool and tap it into the hole with a hammer. For this step, it’s best to start with light force and work your way up so you don’t cause the bolt to become even more stuck. Once the extractor is firmly lodged in the broken bolt shaft, use a wrench to twist it out.
What if none of these methods work?
If all of the methods covered here fail to remove your broken bolt, you’ll most likely have to drill it out completely and then retap the hole. While the methods covered above are complex but doable, this final solution is best reserved for pros and experienced DIYers, especially if it’s on your engine. That’s because tapping a hole is a tricky procedure. Even pros mess it up sometimes, and if you’ve never done it before, it’s best to start on something with lower stakes than your car’s engine.
For this method, the old, broken bolt shaft must be drilled out first. This procedure is somewhat similar to those outlined above in that you’ll start by creating an indentation with a punch tool. Then, it’s a matter of drilling your pilot hole and steadily enlarging it until the broken shaft is drilled out completely. Once the old shaft is drilled out, you’ll have to retap the hole. This step is pretty tricky if you’ve never done it, and you’ll need to ensure that you select the proper tap, which means you need to know a little bit about thread pitch. Explaining the ins and outs of tap and die tools is beyond the scope of this article. However, we will quickly explain how to tap a hole.
Apply a healthy amount of oil to combat the friction. Then, line your tap up perfectly straight, apply downward pressure, and begin turning it slowly. Screw it half a turn forward and then one-quarter turn backward. Follow this procedure until the tap breaks through to the other side or bottoms out. Then, clean the threads and test the hole using your new bolt.